This episode features an in-depth look at the Perlan Project. The mission of the Perlan Project is to fly an engineless aircraft to the edge of space, in this case, by taking advantage of an aerodynamic phenomenon known as wave lift. Not only is soaring to 90,000 feet an audacious goal, but on top of that, the Perlan Project is a worldwide collaborative project run entirely by aviation enthusiasts, scientists, engineers and adventurous pilots. No one has ever soared to the edge of space in a glider and so the Perlan engineers are venturing into unchartered aviation territory on their own. On this episode of the Aerospace Engineering Podcast I speak to Project Manager Morgan Sandercock and Flight Test Engineer Alan Lawless about:
- the genesis and history of the Perlan Project
- how one goes about designing, manufacturing and testing a glider that is to fly to the edge of space
- past success stories
- and the team’s future plans for breaking aviation records.
In case you personally want to support the Perlan Project as a donor, you can do so on the Perlan Project donor page.
If you enjoy the Aerospace Engineering Podcast you can support it by leaving a review on iTunes or by supporting it directly on Patreon, where patrons of the podcast receive exclusive behind-the-scenes content and special episodes. Thanks a lot for listening!
Podcast: Play in new window | Download | Embed
Subscribe: Apple Podcasts | TuneIn | RSS
This episode of the Aerospace Engineering Podcast is sponsored by SAMPE North America. SAMPE is a global professional society that has been providing educational opportunities on advanced materials for more than 70 years. SAMPE’s network of engineers is a key facilitator for the advancement of aerospace engineering by enabling information exchange and synergies between aerospace companies. To find out how SAMPE can help you learn more about advanced materials and process visit SAMPE’s website, or consider attending one of SAMPE’s conferences, such as CAMX, the largest and most comprehensive composites and advanced materials event for products, solutions, networking, and advanced industry thinking.
This episode is also sponsored by StressEbook.com, which is an online hub for you if you are interested in aerospace stress engineering. StressEbook.com provides world-class engineering services and online courses on the stress analysis of aircraft structures, as well as a free ebook and blog. No matter if you’re a junior or senior structural analyst, stressEbook.com provides you with the skills and know-how to become a champion in your workplace.
Selected Links from the Episode
Priyanka Dhopade received her PhD from the University of New South Wales in Canberra, Australia and was the recipient of the Zonta Amelia Earhart Fellowship award, awarded annually to the 35 most outstanding female aerospace PhD students worldwide. Since 2013 she has been researching the thermodynamics of jet engines in the Thermofluids Institute at Oxford University. Priyanka is an expert in computational fluid dynamics modelling of heat transfer, aerodynamics and aero-elasticity in jet engines. She is currently leading the modelling campaigns for various projects in collaboration with industry partners relating to turbine and compressor tip clearance control, turbine internal cooling and active flow control. In this episode, Priyanka and I talk about:
- the challenges of improving the efficiency of current gas turbines
- the intricacies of fluid dynamics modelling
- and a topic particularly close to her heart, the diversity challenge in STEM fields.
If you enjoy the Aerospace Engineering Podcast you can support it by leaving a review on iTunes or by supporting it directly on Patreon, where patrons of the podcast receive exclusive behind-the-scenes content and special episodes. Thanks a lot for listening!
Podcast: Play in new window | Download | Embed
Subscribe: Apple Podcasts | TuneIn | RSS
This episode is brought to you by KDC Resource—the experts in engineering recruitment for the aerospace and defence sector. For more than 15 years, KDC has been matching the very best engineers with the biggest names in the industry; from Airbus Group and GKN Aerospace to Cobham and BAE Systems. KDC’s deep talent pool of aerospace engineers means they are perfectly poised to meet your particular needs with the ideal candidate. In a time of unprecedented engineering skills shortage, KDC Resource will give you an edge over your competitors in the recruitment market.
Selected Links from the Episode
- Priyanka’s research profile at Oxford University
- Oxford Thermfluids Institute
- Turbine Cooling and Design
- Active tip-clearance control (Wiki and NASA)
- What is CFD?
- Women in Engineering at Oxford
- Priyanka on the BBC
- This is Engineering
Dr Mark Cutler has a PhD in Robotics and Autonomous Systems from MIT. He has researched multiple aspects of UAV technology—from designing and building his own novel quadrotor for aerobatic flight to developing machine learning algorithms for autonomous systems. Mark is currently working for the California-based startup Kitty Hawk backed by Google founder Larry Page.
At Kitty Hawk, Mark is applying his expertise in rotorcraft to create the next generation of vehicles for everyday flight. Kitty Hawk are currently designing, testing and building all-electric vertical take-off and landing vehicles for work and play. Their first product, the Cora, is an air taxi that could one day bring us an UBER-like service for the sky, and Kitty Hawk is currently in the first stages of testing the Cora in New Zealand. In this episode of the Aerospace Engineering Podcast, Mark and I talk about:
- his diverse background in UAV’s
- the explosion of hobbyist rotorcraft
- the promises of machine learning for autonomous flight
- and the future of personalised flying
If you enjoy the Aerospace Engineering Podcast you can support it by leaving a review on iTunes or by supporting it directly on Patreon, where patrons of the podcast receive exclusive behind-the-scenes content and special episodes. Thanks a lot for listening!
Podcast: Play in new window | Download | Embed
Subscribe: Apple Podcasts | TuneIn | RSS
This episode is brought to you by KDC Resource—the experts in engineering recruitment for the aerospace and defence sector. For more than 15 years, KDC has been matching the very best engineers with the biggest names in the industry; from Airbus Group and GKN Aerospace to Cobham and BAE Systems. KDC’s deep talent pool of aerospace engineers means they are perfectly poised to meet your particular needs with the ideal candidate. In a time of unprecedented engineering skills shortage, KDC Resource will give you an edge over your competitors in the recruitment market.
This episode is also sponsored by StressEbook.com, which is an online hub for you if you are interested in aerospace stress engineering. StressEbook.com provides world-class engineering services and online courses on the stress analysis of aircraft structures, as well as a free ebook and blog. No matter if you’re a junior or senior structural analyst, StressEbook.com provides you with the skills and know-how to become a champion in your workplace.
Selected Links from the Episode
- Contact Mark through his website
- Mark’s quadcopter on Gizmodo
- Kitty Hawk and career opportunities
- A video of Kitty Hawk’s Cora
- A Tech Insider video on Kitty Hawk’s Flyer
- The New York Times on Kitty Hawk’s flying cars
- A vision for flying taxis
Neil Cloughley is the founder and managing director of Faradair, the UK’s leading hybrid aviation programme. Neil has a broad background in the aviation industry ranging from aircraft re-marketing and aircraft leasing to starting his own aircraft consultancy business, which found him working with the world’s major airlines, OEMs and trailblazing companies like Virgin Galactic. Neil’s father developed one of the most advanced unmanned aerial vehicles of the early 1990s, and had a flying prototype before the General Atomics MQ-1 Predator entered service in 1995.
Unfortunately, as a result of being slightly ahead of its time, and due to a lack of funds and unfortunate timing, ASVEC UK had to close its doors.
Neil is now stepping into his father’s footsteps and building the bio-electric hybrid aircraft (BEHA) drawing from many of the lessons he learned from his father. The BEHA is a six-passenger aircraft with a hybrid gas and electric propulsion system, and is to be used for regional travel of around 200 miles. The BEHA has an unconventional design with a triple-staggered wing, an all-composite airframe and a ducted propeller. These design decisions reflect the three key specifications that need to be met to make regional inter-city flight a reality: minimising noise, emissions and operational costs. In this conversation, Neil and I talk about
- the engineering behind BEHA
- the challenging economics of new aviation businesses
- his long-term vision for a regional Uber-like taxi service in the sky
- and much, much more
If you enjoy the Aerospace Engineering Podcast you can support it by leaving a review on iTunes or by supporting it directly on Patreon, where patrons of the podcast receive exclusive behind-the-scenes content and special episodes. Thanks a lot for listening!
This episode of the Aerospace Engineering Podcast is sponsored by SAMPE North America. SAMPE is a global professional society that has been providing educational opportunities on advanced materials for more than 70 years. SAMPE’s network of engineers is a key facilitator for the advancement of aerospace engineering by enabling information exchange and synergies between aerospace companies. To find out how SAMPE can help you learn more about advanced materials and processes, consider attending the SAMPE 2018 Technical Conference and Expo in Long Beach, California.
Podcast: Play in new window | Download | Embed
Subscribe: Apple Podcasts | TuneIn | RSS
Selected Links from the Episode
- Faradair and the BEHA
- Neil’s vision of an UBER in the sky
- The Journey of an Aerospace Startup — Royal Aeronautical Society lecture
- Profile of Neil Cloughley
- Faradair partnership with Swansea University
- ProDrive’s partnership with Faradair
In this episode I am talking to Lachlan Matchett, who is the VP of Propulsion at Rocket Lab. Rocket Lab is a startup rocket company with the mission of removing barriers to commercial space by frequent launches to low-earth orbit. The current conundrum of many space technology companies that want to launch small satellites into space is that there is no dedicated launch service tailored to their needs. This is where Rocket Lab enters the picture. To provide small payloads with a flexible and dedicated launch vehicle, Rocket Lab has developed the Electron rocket. The Electron is a two-stage rocket that can be tailored to unique orbital requirements and provides frequent flight opportunities at personalised schedules.
In terms of the engineering, there are many interesting features to the Electron rocket, but one of the key innovations is the Rutherford engine that Lachlan Matchett and his team have developed over the last five years. Rutherford is the first oxygen/kerosene-powered engine to use 3D printing for all primary components. In fact, the Rutherford engine can be printed in an astounding 24 hrs, and this is one of the driving factors behind Rocket Lab’s cost efficiency and high target launch frequency. So in this episode, Lachlan and I talk about:
- Rocket Lab’s business model
- their recent launch success in Jan 2018
- some of the engineering highlights of the Rutherford engine
- and Rocket Lab’s plans for the future
I hope that you enjoy this conversation as much as I did. If you enjoy the Aerospace Engineering Podcast you can support it by leaving a review on iTunes or by becoming a patron.
Also, as of this writing Rocket Lab is hiring, so make sure to check out their careers page. You can tune into Rocket Lab’s future launches by following Rocket Lab on Twitter.
What have you learned from this episode? Let me know on Twitter by clicking here.
This episode of the Aerospace Engineering Podcast is sponsored by SAMPE North America. SAMPE is a global professional society that has been providing educational opportunities on advanced materials for more than 70 years. SAMPE’s network of engineers is a key facilitator for the advancement of aerospace engineering by enabling information exchange and synergies between aerospace companies. To find out how SAMPE can help you learn more about advanced materials and processes, consider attending the SAMPE 2018 Technical Conference and Expo in Long Beach, California.
Podcast: Play in new window | Download | Embed
Subscribe: Apple Podcasts | TuneIn | RSS
Selected Links from the Episode
Today’s episode features Dr Valeska Ting who is a Reader in Smart Nanomaterials at the University of Bristol and is researching the use of nanoporous materials for hydrogen storage. Using hydrogen as a fuel source has many benefits. Due to its excellent energy density, hydrogen has long been hailed as an alternative to fossil fuels but it’s also an excellent means of storing renewable energy from solar or wind sources. One of the challenges of storing hydrogen is its low density, meaning that large volumes are required to store efficient amounts of hydrogen to be able to use it as a fuel. This is precisely where Valeska’s research enters the picture. The nanoporous materials that she is working on can increase the density of hydrogen by a factor of a 1000, and therefore provide a key stepping stone towards more efficient hydrogen-powered vehicles. In this episode, Valeska and I talk about multiple aspects of this technology including:
- what nanoporous materials are and how they work
- how they can be used to create multifunctional materials
- what scientific challenges she is addressing to scale-up and improve their performance, and
- how they could be applied to design lighter hydrogen tanks for cars, aircraft or even rockets
I hope that you enjoy this conversation as much as I did. If you enjoy the Aerospace Engineering Podcast you can support it by leaving a review on iTunes or by becoming a patron.
What have you learned from this episode? Let me know on Twitter by clicking here.
This episode of the Aerospace Engineering Podcast is sponsored by SAMPE North America. SAMPE is a global professional society that has been providing educational opportunities on advanced materials for more than 70 years. SAMPE’s network of engineers is a key facilitator for the advancement of aerospace engineering by enabling information exchange and synergies between aerospace companies. To find out how SAMPE can help you learn more about advanced materials and processes, consider attending the SAMPE 2018 Technical Conference and Expo in Long Beach, California.
Podcast: Play in new window | Download | Embed
Subscribe: Apple Podcasts | TuneIn | RSS
Selected Links from the Episode
On this episode of the podcast I speak to Mike Lawton, who is the founder and CEO of Oxford Space Systems (OSS). OSS is an award-winning space technology company that is developing a new generation of deployable space structures that are lighter, simpler and cheaper than current products on the market. These deployable structures deploy antennas and solar panels on satellites orbiting earth, and are tricky to design because they need to package to a fraction of their deployed size, and need to be as lightweight as possible. OSS’ first product, the AstroTube boom, was launched into space and deployed on a cubesat in September 2016. This achievement set a new industry record in terms of development time, going from company formation to orbit in under 30 months. I met Mike at the OSS design office to talk about:
- venture capital funding of NewSpace companies
- how the design philosophy of NewSpace companies differs from established firms
- how origami, the Japanese art of folding, is being used to design more efficient deployable structures
- the flexible composites technology that OSS are developing
- and his vision for the future of space commercialisation
I hope that you enjoy this conversation as much as I did. If you enjoy the Aerospace Engineering Podcast you can support it by leaving a review on iTunes or by becoming a patron.
This episode of the Aerospace Engineering Podcast is sponsored by SAMPE North America. SAMPE is a global professional society that has been providing educational opportunities on advanced materials for more than 70 years. SAMPE’s network of engineers is a key facilitator for the advancement of aerospace engineering by enabling information exchange and synergies between aerospace companies. To find out how SAMPE can help you learn more about advanced materials and processes, consider attending the SAMPE 2018 Technical Conference and Expo in Long Beach, California.
Podcast: Play in new window | Download | Embed
Subscribe: Apple Podcasts | TuneIn | RSS
Selected Links from the Episode
- Oxford Space Systems:
- Technology overview
- AstroTube
- AstroHinge
- Origami and unpacking in space (Part 1, Part 2)
- First product launch
- Harwell Space Cluster
- Catapult Satellite Applications
- NewSpace
- UK Space Agency Funding
- Prof. Zhong You, Oxford University
- Asteroid mining
In this episode I am talking to John Britton. John was the chief engineer of Concorde on the British side of the enterprise from 1994 until Concorde’s demise in 2003. John possesses a wealth of knowledge regarding the engineering behind Concorde, and its heritage in Bristol, UK. Because he was the chief engineer at its demise, he also has a unique insight into why the aircraft is no longer flying today. In this conversation, John and I talk about:
- how he ended up as the Chief Engineer of Concorde
- what engineering feats made Concorde special
- why Concorde is no longer flying today
- and what he thinks new supersonic companies need to focus on
This interview was recorded at Aerospace Bristol, which is a new aerospace museum located at Filton Airfield in the South West of the United Kingdom. From the beginnings of powered flight, Filton Airfield was the birthplace of many a flying machine – from aeroplanes and helicopters to missiles and satellites. Aerospace Bristol represents the new heart to the area’s aerospace heritage.
I hope that you enjoy this conversation as much as I did. If you enjoy the Aerospace Engineering Podcast you can support it by leaving a review on iTunes or by becoming a patron.
This episode of the Aerospace Engineering Podcast is sponsored by SAMPE North America. SAMPE is a global professional society that has been providing educational opportunities on advanced materials for more than 70 years. SAMPE’s network of engineers is a key facilitator for the advancement of aerospace engineering by enabling information exchange and synergies between aerospace companies. To find out how SAMPE can help you learn more about advanced materials and processes, consider attending the SAMPE 2018 Technical Conference and Expo in Long Beach, California.
Podcast: Play in new window | Download | Embed
Subscribe: Apple Podcasts | TuneIn | RSS
Selected Links from the Episode
- Aerospace Bristol museum
- Heritage of Filton Airfield
- Sir George White
- The Bristol Aeroplane Company
- British Aircraft Corporation
- Concorde:
- Timeline
- The Concorde Story documentary
- Powerplant, fuel system, wing and skin temperatures
- The demise of Concorde: video and article and another article
- The Concorde rival: Tu-144
- Overview
- The Paris Crash (ironic that Concorde too would crash in Paris 30 years later)
- Return of supersonic commercial flights with:
“We need to get going into the future in terms of clean aviation” — Kim-Tobias Kohn
On this episode of the podcast I speak to Kim-Tobias Kohn who is a lecturer in Aerospace Engineering at the University of the West of England. Beside his main vocation, Kim is also an avid pilot and runs an electric skateboard startup company. Kim has garnered attention in the media and from aerospace societies in the UK for his unique university project of building an electric glider with his undergraduate students. For obvious reasons, building an electric passenger aircraft that can replace current fuel-powered airliners is significantly more challenging than replacing gasoline cars with electric vehicles. However, there is a growing grass-roots initiative developing in the UK that is attempting to solve some of the regulatory and technical challenges to realise this vision of electric aviation.
So in this episode Kim and I talk about:
- the unique regulatory framework for experimental aircraft in the UK known as the E-conditions
- the major technical hurdles that need to be overcome to make electric aviation a reality
- how the UAV/drone sector is opening doors for larger-scale electric aviation
- his university project of building an electric glider
- his dreams for a student-led design, build and fly competition for electric aircraft
- and much, much more
I hope that you enjoy this conversation as much as I did. If you enjoy the Aerospace Engineering Podcast you can support it by leaving a review on iTunes or by becoming a patron.
What have you learned from this episode? Let me know on Twitter by clicking here.
This episode of the Aerospace Engineering Podcast is sponsored by SAMPE North America. SAMPE is a global professional society that has been providing educational opportunities on advanced materials for more than 70 years. SAMPE’s network of engineers is a key facilitator for the advancement of aerospace engineering by enabling information exchange and synergies between aerospace companies. To find out how SAMPE can help you learn more about advanced materials and processes, consider attending the SAMPE 2018 Technical Conference and Expo in Long Beach, California.
Podcast: Play in new window | Download | Embed
Subscribe: Apple Podcasts | TuneIn | RSS
Selected Links from the Episode
- Kim’s electric glider project and his YouTube Vlog
- Kim’s company emotion engineering (UAV’s, electric skateboards and aerial photography)
- More info from the University of the West of England about the undergraduate electric glider project
- Royal Aeronautical Society on electric flight
- The UK E-conditions
- Airbus, Rolls Royce and Siemens E-fan hybrid electric aircraft
- EasyJet on electric aircraft
- Wired on electric aircraft
- Electric flight potential and limitations
- Formula Student and Formula SAE
- SolarFlight solar-powered planes
- Boeing 787 Dreamliner battery problems
Over the last couple of months, a number of readers of the blog and listeners of the podcast have asked me about my research. Although there is a brief overview on the Contact page, the information there probably leaves too many things unsaid to form a clear picture of what the research group I am part of is trying to achieve. On the other hand, going into the nitty-gritty details of the mathematical models, computer methods and prototypes that we are developing will probably bore most readers of this blog senseless. In fact, communicating the technical details of research is often counterproductive when creating awareness with colleagues, the general public and funding bodies.
The power of stories
A much more effective way of communicating one’s ideas is through stories. For many centuries, stories were the predominant means of understanding life and society. Orators, poets and philosophers used analogies, metaphors and fables as arguments that voiced something important about reality. In this way, literature is not mere wordplay, but an effective means of communicating a complex topic in a manner that sticks, often with recourse to emotion. There is even evidence to suggest that stories have evolutionary utility, by being a means to relay important information such as a lucrative hunting spot. This hypothesis would suggest that a proclivity for stories is hardwired into our psyche. Some people, like Jonathan Gottschall, even argue that we live our entire lives by projecting a web of stories over everything we perceive through our senses.
In many ways, the great achievement of the Enlightenment, and Western thought in general, is a devotion to rationality: I don’t want to hear the story, give me the numbers instead. In his biography of Steve Jobs, Walter Isaacson argues that rational thought is not an innate human characteristic as such, but rather needs to be learned. Engineers—at least the good ones—should have plenty of this training. And perhaps this training is why we generally have a hard time communicating our ideas through stories—sticking rather to the technical details, which, generally speaking, tend to be a lot less inspiring.
Taking inspiration from nature: shape-adaptation
So what I will attempt to do in this post is to relay some of the technical details of our research through a vision of the future—a story of science-fiction if you will. It is a vision of shape-adaptive aircraft that can radically re-configure their shape as the operating conditions around them change.
Engineering systems are typically designed to meet multiple specifications stemming from (i) different functions that the system is meant to fulfil and (ii) the broad spectrum of environments it is operating in.
In terms of functionality, the most efficient approach is combining as many functions into one system as possible—so-called multi-functionality. For example, the wings of early aircraft such as the Wright Flyer, had two mechanisms for resisting aerodynamic loads and providing lift. The strut-and-wire-braced box truss provided bending rigidity and torsional stiffness against excessive wing bending and wing twisting, while the fabric wing skins provided the aerodynamic profile. The structural and aerodynamic functions were separated into two systems, and neither contributed to the other. In modern, stressed-skin designs, the externally visible wing skin serves both as an aerodynamic profile and also provides structural support.
When the operating conditions around an aircraft change, the situation is a bit more complicated. In isolation, different conditions can push the design in opposite directions, meaning that some form of design compromise is needed. The disadvantage of a compromise is that the aircraft will perform sub-optimally in most, if not all, of the individual operating conditions.
A solution to this conundrum is adaptation, also known as morphing, which would allow structures to change geometry and/or material properties in response to changing conditions. As with many good ideas we can take inspiration from nature. For example, birds can adapt the camber and angle of attack of their wings to react to different flight conditions. On modern aircraft wings, leading-edge slats and trailing-edge flaps, which are used to increase the lift-generating capabilities of wings at slow airspeeds, crucial for landing and takeoff, are manifestations of such adaptation. Even though these devices are effective and reliable, they rely on ancillary devices, such as heavy hydraulic or electric actuators, to facilitate the wing shape adaptation. By flexing and relaxing their wing muscles, birds have the ability to adapt between many different wing configurations, and due to the information-processing capability of the nervous system, this happens quickly and on the fly.
Hence, the challenge for engineers is how to embed shape-adaptive technologies in a multi-functional manner. And ideally, we would want both the actuation (think muscles), sensors (think nerves) and information processing (think brain) to be integral to the materials or structure. Only in this way will it be possible to design seamless and aerodynamically efficient aircraft that have the ability of sentient organisms to adapt to a wide array of changing environments.
An historic aside
The biomimetic inspiration for morphing and adaptive technologies has been around since the dawn of powered flight. This is no surprise given that many of the early aircraft pioneers took their inspiration from nature—dissecting bird wings and observing birds in flight to borrow ideas for steering and control. For example, the Wright Flyer used flexible wingtips that could be warped using pulleys and cables. Even though this technique became known as wing warping, it is essentially a basic form of wing morphing.
In the 1910-1920s many patents about variable camber wings, telescopic wings and variable angle-of-attack wings were filed, but none of these concepts made it into production. This can partly be explained by the shift from a more compliant timber and fabric construction to a stiffer metallic design. This allowed for greater flying speeds and bigger aircraft, but increased the energetic threshold required for shape adaptation. Interest in morphing aircraft intensified in the post-WWII era, when the technological race between the USA and the USSR provided the impetus for many novel ideas. One example, the Bell X-5, featured variable wing sweep in flight. Wing sweep reduces the effective airspeed across the lifting surface and can therefore be used to prevent supersonic shocks—a source of parasitic drag. The faster you want to fly, the greater the required sweep, and hence this adaptive feature allowed the X-5 to fly more efficiently at subsonic and supersonic speeds. The same concept was successfully implemented in the MiG-23, Grumman F-14 and Rockwell B-1B. Apart from moving slats, flaps and control surfaces present on most aircraft today, the most prominent modern example of morphing is probably the drooping nose of the Concorde, which was used to find a compromise for better cockpit visibility during landing and streamlining at cruise.
These early morphing ideas revolve predominantly around mechanically operated devices. That is, multiple components are joined by a mechanical hinge and the different components are then moved relative to each other by an actuator. Starting from the 1990s, new developments in materials science catalysed a shift from mechanical devices to novel materials. For example, during the late 1990s NASA Langley and DARPA led the Morphing Project and Smart Wing programme, which led to wing prototypes with gapless and hingeless leading- and trailing-edge control surfaces. NASA also released its now renowned artist impression of a morphing aircraft set in the year 2030, with wings that are capable of sweeping back and forth, changing shape and with compliant feather-like control surfaces for extreme manoeuvres.
Over the last 20 years, lots and lots of different materials have been used for a range of morphing technologies and concepts. Many of these technologies, ranging from flexible elastomers and honeycomb-type auxetic materials, to deployable structures and shape-memory metals, are summarised in the excellent review paper by Thill et al. from 2008. One particular concept, the FlexSys Mission Adaptive Compliant Wing (MACW), which has a moveable internal structure covered by a flexible skin and is capable of morphing the trailing edge through an angle of 20°, has been undergoing extended flight tests. One of these tests on the Scaled Composites SpaceShipOne suggests that the MACW could lead to 15% in fuel savings due to an improved laminar flow profile and minimal flow separation.
A shift in perspective: Well-behaved non-linearity
To most engineers, non-linearity is something to avoid. In a linear system, cause and effect are proportional—if I apply a force of 100 N to a beam and it bends by 1 mm, then I can expect it to bend by 2 mm for a force of 200 N and 4 mm for a force of 400 N. What is more, for a more complex situation with many interacting parts, a linear system is always a simple addition of its parts. This means a multi-part system can be broken apart, its constituents analysed individually, and the behaviour of the whole system deduced from an aggregation of the constituents. This linear decomposition is not possible for a non-linear system, which means that (i) non-linear systems are more complicated and costly to analyse, and (ii) the non-linearity can lead to unwanted and counter-intuitive effects.
One example of structural non-linearity is an instability. In aerospace engineering, minimising mass is the main design driver for more efficiency. No matter if you are trying to hold an aircraft aloft or shooting a rocket into space, the lighter your machine, the easier your task. This drive for lightweighting leads to thinner and thinner structures, where instabilities (like buckling) play a greater and greater role. In general, buckling is the tendency of thin-walled structures (struts and plates) loaded in compression to spontaneously bow out-of-plane (bend) at a critical value of compression. The buckling load varies with the cube of the strut’s or plate’s thickness, and while minimising thickness is very effective for reducing mass, it means that the susceptibility to buckling shoots up very quickly. Buckling is a non-linear event because the structure fundamentally changes its deformation mode—from one involving only compression, to one involving bending. Because there was no bending component pre-buckling, the bent post-buckling state cannot be a simple aggregation of pre-buckled states, and hence the phenomenon must be non-linear.
In traditional engineering design, buckling is considered as an unwanted “failure” mode to be treated no differently than material fracture, fatigue or plastic deformation. This traditional view is for good reason because buckling can cause a structure to lose its stiffness, and in the worst case, collapse. However, seen in a different light, the change in deformation mode brought on by buckling, can also be viewed as an opportunity for well-behaved shape-adaptation.
This concept can be illustrated using an example that will be familiar to most people who have sat through an introductory mechanics course as an undergrad—the Euler strut pictured above. Take a thin strut and pin the two ends so that they cannot move perpendicular to the strut axis. Then apply a compressive load by moving the two ends closer together. For an idealised strut with no geometric imperfections and with the load perfectly aligned with the strut axis, the strut will remain flat and simply compress. At a critical value of the applied load, the strut will suddenly bow out-of-plane, i.e. bend into one of two mirror-symmetric sinusoidal shapes. By applying a load perpendicular to the strut axis, the structure can now be snapped from one sinusoidal shape to another. This is indeed a pronounced snap, whereby the strut needs to be actively pushed in the direction of the other shape, but once a critical point is reached (a so-called tipping point), the strut suddenly and automatically transitions to the other shape without any further expenditure of energy. And once the load is removed, the structure will happily stay in this second configuration.
This is known as as bi-stable structure because there are two distinct configurations, which are both stable under no applied transverse load. These bi-stable systems are attractive for shape-adaptation, because to facilitate the shape change, energy only has to be expended to reach the snapping point, and thereafter the structure will happily settle into the second configuration.
Of course, this system is rather simple and these two sinusoidal shapes are not directly useful for the large spectrum of shape-adaptations we would want to achieve for real aircraft structures. However, even for this simple example, the design space is relatively large because the two strut ends can be moved or rotated relative to each other such that the initial shape of the strut is no longer flat but curved. In this manner, a wide array of different configuration pairs is attainable. Furthermore, by varying the degree of compression the post-buckled strut can be designed so that one of the two configurations is unstable if the snapping load is removed. This means that the structure can be snapped from an initially curved shape into another, and when the transverse load is removed, the strut will automatically snap back to its previous shape. This is generally known as a monostable snapping device.
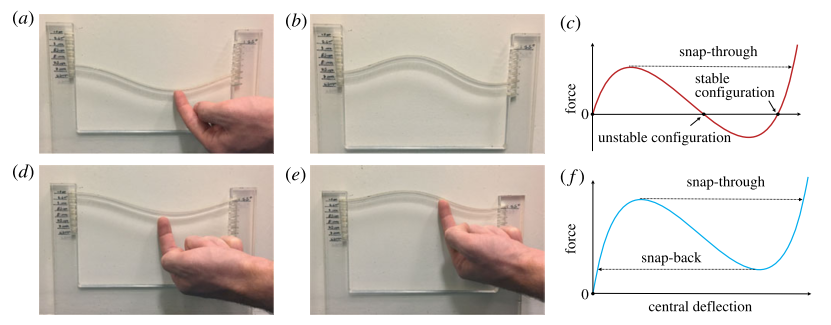
Multistability and snap-through. (a) The application of a transverse load causes snap through into the inverted stable shape (b). (c) The applied load increases until it reaches a critical value. At this point, the beam snaps through a region of instability, where applied load decreases, reaching a second stable branch. Upon load removal, the structures settles in the secondary stable state. Similarly, a monostable buckled structure snaps from its first (d) to its second inverted configuration (e) when a transverse load is applied, but, as shown in (f), load removal causes snap back to the original unloaded equilibrium (d). Reproduced from Arena et al. (2017) Adaptive compliant structures for flow regulation. Proc.R.Soc.A 473: 20170334
Hence, from these general concepts illustrated via a small toy model, it follows that it is possible to take advantage of concepts such as bi-stability and snap-through instabilities to induced repeatable and well-behaved shape changes.
An example: a shape-adaptive air inlet
The multi-stable behaviour described above can, for example, be used to design an adaptive air inlet for engine cooling on car bonnets or jet engine covers. In this situation, you generally want the air inlet to be open at low velocities to maximise the air flow into the engine. At higher velocities, however, enough air is impinging onto the hot parts of the engine that these additional cooling ducts can be closed to reduce the induced drag.
Consider, for example, the schematic air inlet in the figure below and assume that it is designed to be fully open at low air speeds. Considering the tradeoff between cooling performance and drag described above, at a critical air speed we would like the air inlet to automatically snap-shut for drag reduction. Furthermore, once the air-speed increases, the air inlet should open-up again to facilitate cooling. Ideally, this mechanism is to be designed autonomously without recourse to additional sensors or actuators. In fact, the fluid flow over the inlet creates a pressure field which can be used to actuate the adaptive air inlet, and the amount of compression of the inlet, i.e. the post-buckled state, plays the role of an integral sensing and control system.
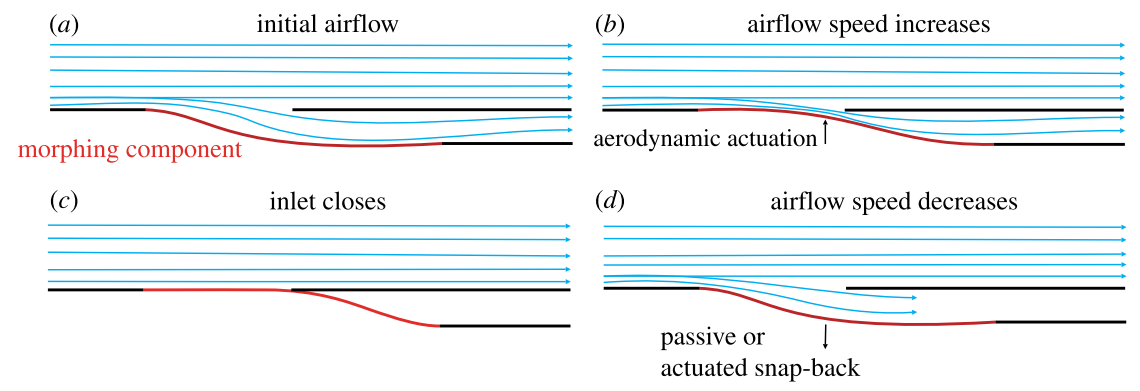
Reproduced from Arena et al. (2017) Adaptive compliant structures for flow regulation. Proc.R.Soc.A 473: 20170334
An increase of fluid velocity into the inlet generates an area of low static pressure over the adaptive component. This pressure field is equivalent to a transverse load described above and causes the adaptive component to be sucked upwards. At a critical velocity, the low static pressure field exceeds the tipping point and the inlet snaps shut. If the device is designed to be bistable, then an additional actuation device is required to open the inlet up again. However, if the inlet is a monostable snapping device, then it will automatically open again once the airspeed is reduced and falls beneath a certain threshold. In this manner, a non-linear snapping air inlet can be used to automatically open and close a cooling duct purely by interacting with the fluid around it.
In our lab we have built and successfully tested such an adaptive air inlet in a wind tunnel. The two options of bistable and monostable snapping behaviour are clearly visible in the video below. Our current research is looking into the question of whether this behaviour can be extended from bistability to multi-stability. This would allow us to introduce an intermediate stage between the fully open and closed states for reduced air flow into the duct.
The question of control
The shape-adaptive air inlet is an example of a passive morphing device. Passive control refers to the ability of a system to react and adapt to external stimuli without having additional sensory, information processing or actuating devices. For example, no pressure sensors were attached to the air inlet to provide a signal to an external actuator to close the duct. Instead, the sensing, actuating and control functions were entirely embedded within the non-linear mechanics of the air inlet. The pressure field provided the actuation, the tipping point acted as an on/off switch, and the inherent stability of the second configuration acted as control. Such passive control systems are attractive from a minimal design perspective, and nature has found uses for passive control in the ruffling of birds’ feathers and adaptive shark scales for boundary layer control.
However, most shape-adaptive systems in nature are of the active type, where sensors (nerves) provide information to a central information processing unit (brain), which then provides an action signal to actuators (muscles). The beauty of biological organisms, may they be birds or even “smart” plants like the Venus flytrap, is that the entire control system of sensing, information processing and actuating is very efficiently contained within the organism. For example, the modern control systems of hydraulic lines and actuators that drive slats, flaps and control surfaces on an aircraft seem clumsy compared to the integral and lightweight solutions that evolution has crafted.
Of course, nature has undergone 4 billion years of evolution to arrive at these solutions, and so it is no wonder that our systems are comparatively ad hoc. But what seems crucial is that the three functions of sensing, information processing and actuation need to be scaled down, distributed more evenly and integrated tightly within the surrounding structure. Consider the musculoskeletal system of your arms, which can be understood as a tightly layered system. You have bones to provide structure, muscles layered on top for actuation, nerves running through muscles as lines of communication, and a further layer of skin to contain everything and provide sensory means to probe your surroundings (touch and heat).
Focusing on this concept of a layered structure, only in the last 1-2 decades have we gained the manufacturing expertise to produce such structures and materials with fidelity. Classic manufacturing techniques are subtractive in nature. Take a big billet of metal and cut everything away which is not your desired object. Contrast this to the modern additive manufacturing techniques of 3-D printing and laminated composite materials. Here, you create an object by layering material bit by bit, creating the whole unit from the bottom up. In the case of 3-D printing, a nozzle ejects material in pre-defined paths, whereas advanced composite laminates are manufactured by stacking layers of fibre-reinforced plastic on top of each other. Both these manufacturing techniques have the unique possibility of combining different material systems on the go, and even inserting additional components throughout the manufacturing process.
For example, consider an analogue to your arm renditioned as multiple material layers. Take a couple layers of carbon fibre composite to provide structure, layer on top of that a layer of magnetostrictive or piezo-electric material as a muscle and a layer of modern thin-film integrated circuitry. Hold everything together by a soft, impact resistant layer studded with sensors, and voilá, there goes your cyborg arm. Of course, this is a dramatic over-simplification of a potential solution, and to date, entirely science fiction. But the utility of this thought experiment is to plant a flag somewhere ambitious, which can then serve as a motivating goal. We might not arrive at this precise reality in the future, but the technology that will be developed just by embarking on this journey will certainly be novel and exciting.
Conclusion
So here you have it: a vision for the future of shape-adaptive aircraft featuring smart and multi-functional materials/structures. Advances in material science, manufacturing technology and compliant integrated circuitry now allow us to embed intelligence into engineering structures. This means structures will no longer just resist loads but have other integrated functions like sensing, information processing and actuation embedded within them. Furthermore, appreciable shape changes imply a degree of non-linearity and the shift from avoiding non-linearity to exploiting it for novel functionality opens up an entirely new frontier for innovation.
Acknowledgements
As with most modern research, there is a group of engineers working on these ideas, and I am just one member of this group at the Bristol Composites Institute. The people involved in this project are Alberto Pirrera, Paul Weaver, Gaetano Arena, Raf Theunissen and Alex Brinkmeyer. The work on the adaptive air inlet was funded by the Engineering and Physical Sciences Research Council (EPSRC).
Further Reading
- NASA – Go, Go, Green Wing! Mighty Morphing Materials in Aircraft Design
- NASA – NASA Successfully Tests Shape-Changing Wing for Next Generation Aviation
- T. A. Weisshaar (2006) – Morphing Aircraft Technology – New Shapes for Aircraft Design
- Arena et al. (2017) Adaptive compliant structures for flow regulation. Proc.R.Soc.A 473: 20170334
Sign-up to the monthly Aerospaced newsletter
Recent Posts
- Podcast Ep. #49 – 9T Labs is Producing High-Performance Composite Materials Through 3D Printing
- Podcast Ep. #48 – Engineering Complex Systems for Harsh Environments with First Mode
- Podcast Ep. #47 – Möbius Aero and MμZ Motion: a Winning Team for Electric Air Racing
- Podcast Ep. #46 – Tow-Steered Composite Materials with iCOMAT
- Podcast Ep. #45 – Industrialising Rocket Science with Rocket Factory Augsburg
Topics
- 3D Printing (4)
- Aerodynamics (29)
- Aerospace Engineering (11)
- Air-to-Air Refuelling (1)
- Aircraft (16)
- Autonomy (2)
- Bio-mimicry (9)
- Case Studies (15)
- Composite Materials (25)
- Composites (7)
- Computational Fluid Dynamics (2)
- Contra-Rotation (1)
- Design (2)
- Digitisation (2)
- Drones (1)
- Education (1)
- Electric Aviation (11)
- Engineering (23)
- General Aerospace (28)
- Gliders (1)
- Helicopters (3)
- History (26)
- Jet Engines (4)
- Machine Learning (4)
- Manufacturing (12)
- Military (2)
- Modelling (2)
- Nanomaterials (2)
- NASA (2)
- New Space (11)
- News (3)
- Nonlinear Structures (1)
- Novel Materials/Tailored Structures (14)
- Personal Aviation (5)
- Podcast (45)
- Propulsion (9)
- Renewable Energy (2)
- Renewables (1)
- Rocket Science (17)
- Satellites (8)
- Shape Adaptation (1)
- Smart Materials (1)
- Space (12)
- Space Junk (1)
- Sport Airplanes (2)
- Startup (19)
- STOL (1)
- Structural Efficiency (5)
- Structural Mechanics (1)
- Superalloys (1)
- Supersonic Flight (2)
- Technology (18)
- UAVs (2)
- Virtual Reality (2)
- VTOL (3)
- Privacy & Cookies: This site uses cookies. By continuing to use this website, you agree to their use.
To find out more, including how to control cookies, see here: Cookie Policy